Manufacturing Information Technology Standardization Reference architecture
IVIはものづくりとITが融合したあたらしい社会をデザインし、モノと情報を介した人と人との係り方、作る人と使う人との関係性をあらためて問い直し、よりよいバリューが世界の隅々に行きわたるしくみづくりを目指しています。
Latest news
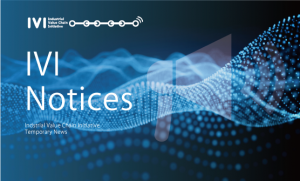
IVIつながるものづくりアワード2025決定!“人作業のミスゼロ化”への挑んだWGが最優秀賞を受賞
インダストリアル・バリューチェーン・イニシアティブ(理事長 西岡 靖之 工学博士、以下IVI)は、2025年6月12日にIVIつながるものづくりアワード2025の審査結果を発表しました。2024年度に活動した12の業務シ
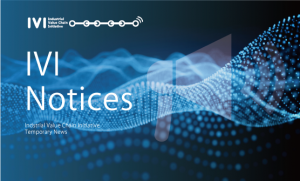
【プレスリリース】製造業PLMの共通モデルの国際化へ向けた取組をスタート
一般社団法人インダストリアル・バリューチェーン・イニシアティブ(理事長 西岡靖之 法政大学教授、以下IVI)は、国内のPLM開発企業らとともに、製品ライフサイクル管理(PLM)を製造業全体に拡張した「製造業PLM」の共通
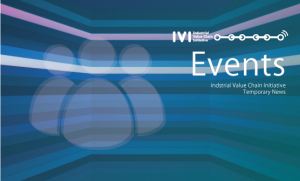
【-終了-】IVI設立10周年イベント&レセプションのご案内
IVI設立10周年イベント ―分断が進むデジタル社会の処方箋― インダストリアル・バリューチェーン・イニシアティブ(IVI)はものづくりとITが融合した新しい社会をデザインし、つながるものづくりによってバリューが世界の隅
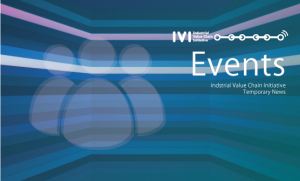
【-終了-】IVIソリューションセミナー2025(5/8)のご案内
IVIは、5月8日に「IVIソリューションセミナー2025」を開催いたします。本セミナーはIVI会員向けのイベントとなりますが、IVI非会員(IVIの活動に関心のある方、製造業のDX担当者を想定)の方もご参加可能です。概
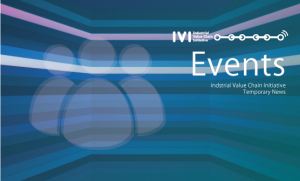
【-終了-】DXなんて怖くない!!第2弾ミニシンポジウム2025(IVI教育普及委員会主催)
IVI教育普及委員会は、「DXなんて怖くない!第2弾ミニシンポジウム2025」を5月15日に開催します。完全オンライン配信で参加無料となりますので、ぜひご参加ください。 昨年に続く2回目のシンポジウム 3つの「推し」!
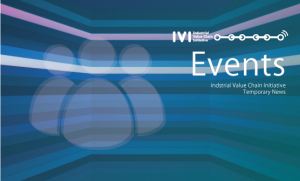
【受講申込受付中】2025年度「MMITものづくりDX指導者育成講座」受講申込開始のお知らせ
IVIは製造業のDXで中核となる工場のデジタル化、データ化を推進するリーダを育成する2025年度「MMITものづくりDX指導者育成講座」の受講申込の受付を4月10日より開始しました。全10回の講座で、ものづくりに関するさ
Event
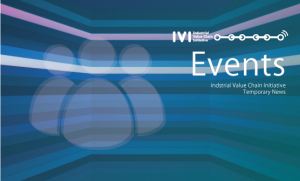
【-終了-】IVI設立10周年イベント&レセプションのご案内
IVI設立10周年イベント ―分断が進むデジタル社会の処方箋― インダストリアル・バリューチェーン・イニシアティブ(IVI)はものづくりとITが融合した新しい社会をデザインし、つながるものづくりによってバリューが世界の隅
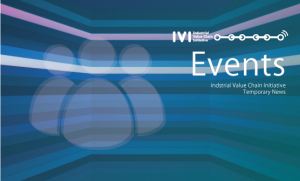
【-終了-】DXなんて怖くない!!第2弾ミニシンポジウム2025(IVI教育普及委員会主催)
IVI教育普及委員会は、「DXなんて怖くない!第2弾ミニシンポジウム2025」を5月15日に開催します。完全オンライン配信で参加無料となりますので、ぜひご参加ください。 昨年に続く2回目のシンポジウム 3つの「推し」!
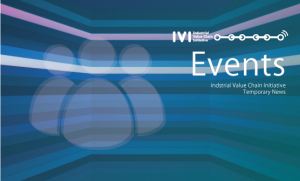
【受講申込受付中】2025年度「MMITものづくりDX指導者育成講座」受講申込開始のお知らせ
IVIは製造業のDXで中核となる工場のデジタル化、データ化を推進するリーダを育成する2025年度「MMITものづくりDX指導者育成講座」の受講申込の受付を4月10日より開始しました。全10回の講座で、ものづくりに関するさ
About US
IVI (Industrial Value Chain Initiative)とは
Industrial Value Chain Initiative (インダストリアル・バリューチェーン・イニシアティブ)は、ものづくりとITが融合したあたらしい社会をデザインし、あるべき方向に向かわせるための活動において、それぞれの企業のそれぞれの現場が、それぞれの立場で、等しくイニシアティブをとるためのフォーラムです。
IoTや自動化技術、ネットワーク技術など、高度で先端的な要素技術が時代を大きく変えようとしているなかで、得てして忘れてしまいがちな“人”の存在をあえてクローズアップし、人が中心となったものづくりが、IoT時代にどのように変わるか、変わるべきかを議論します。
ITによって、モノと情報を介した人と人との係り方、作る人と使う人との関係性を、あらためて問い直し、バリューが世界の隅々に行きわたるしくみを目指します。
- OUR MISSION -
MISSION1
ボトムアップなアプローチによる“つながるものづくり”の為のエコシステムの作成
MISSION2
ゆるやかな標準を共有するしくみによりものづくりの知識やノウハウの価値化
MISSION3
オープンとクローズのバランスの中で協調と競争のためのルールづくりへの貢献
IVI会員について
※2023 年3 月 31 日時点
会員企業
※幹事企業
会員メリットについて
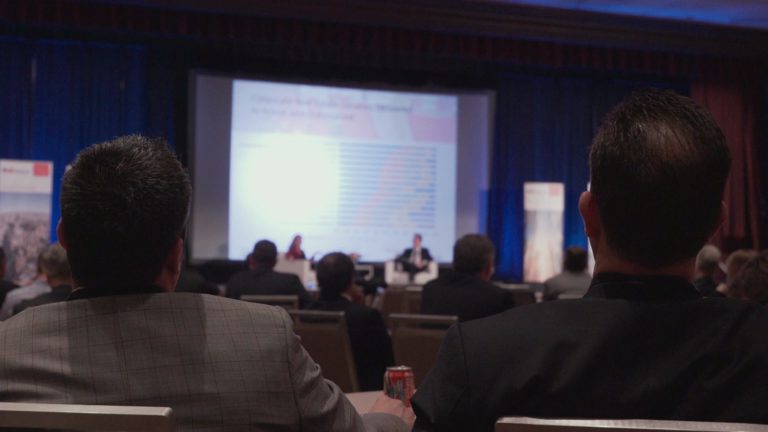
01.様々な活動へメンバーとして参加
業務シナリオWGやASGをはじめとする様々な活動にメンバーとして参加できます。
また会員限定セミナー(不定期開催)への参加ができます。過去にはMoUを締結している米国企業を中心とした産業団体「インダストリアル・インターネット・コンソーシアム(IIC)」との共催で事例共有セミナーを開催しました。
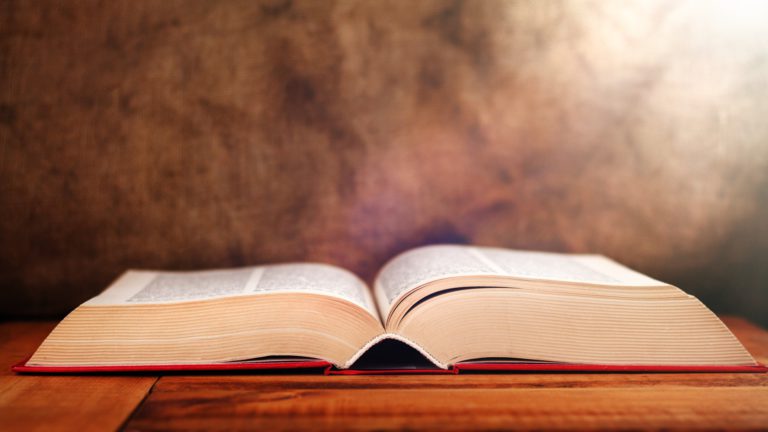
02.業務シナリオ事例集
WG活動や、ASG活動などといった様々な活動へ参加可能毎年発行している業務シナリオ事例集を無料で配布しています(定価3万円)
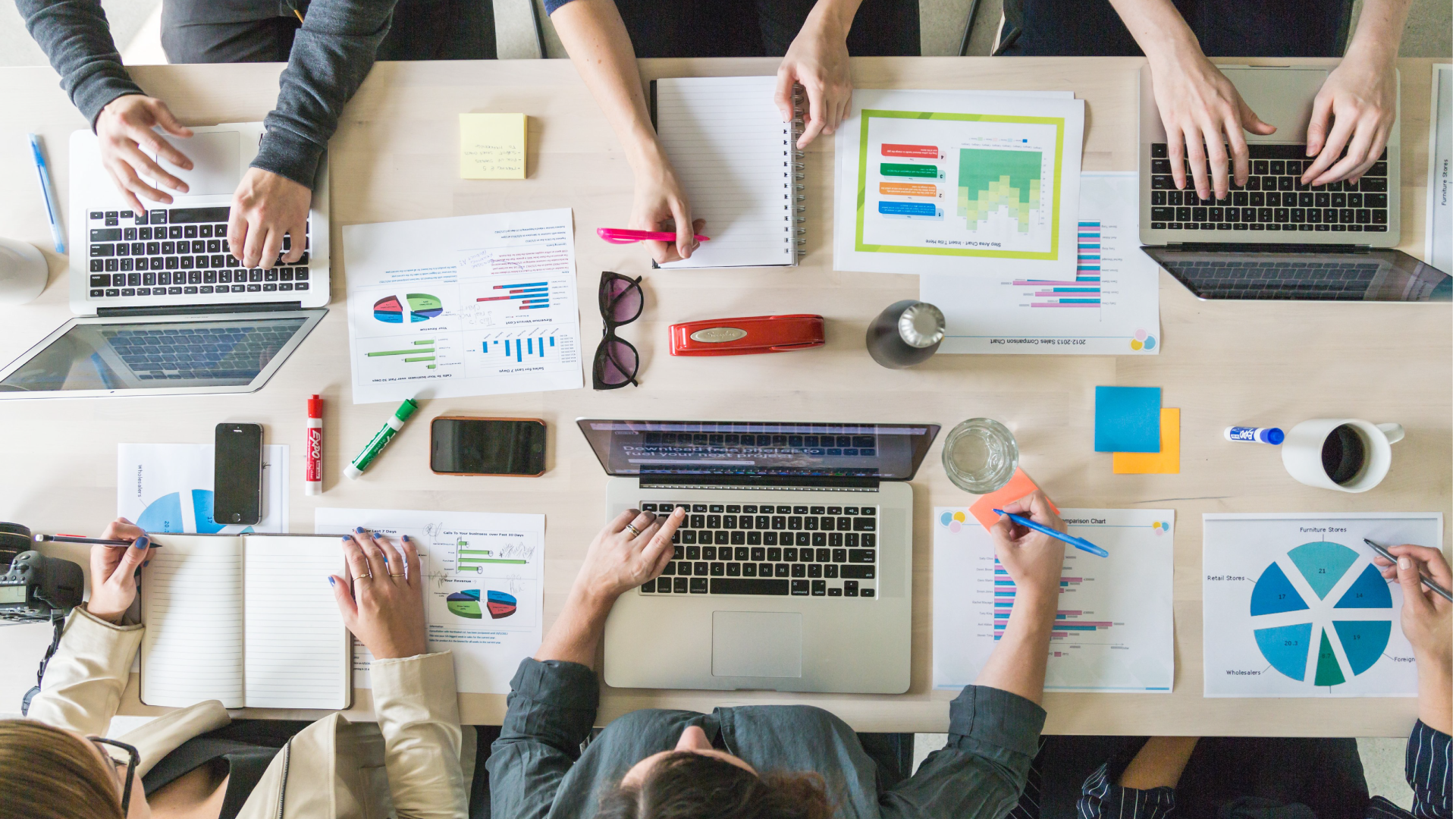
03.各種イベントへの優待
IVIが年に2回開催しているシンポジウムに優先的に申込ができます。またシンポジウムが有料の場合は、入会口数に応じて無料でシンポジウムへの参加が可能です。
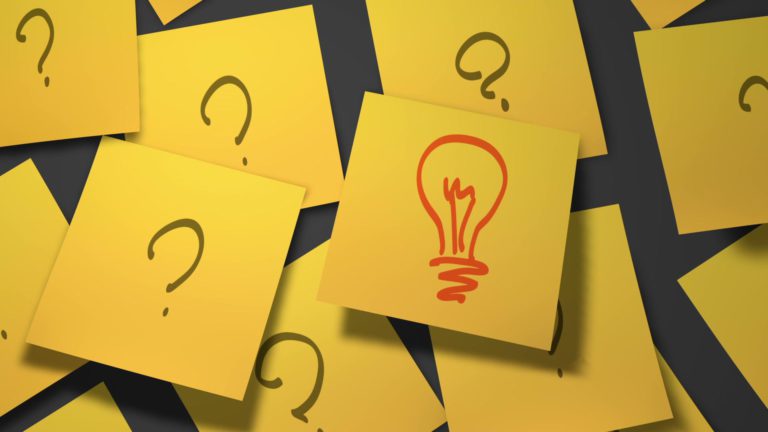
04.各種情報収集
IoTやDXを推進する各種活動を行っており、メンバーとして参加することにより、各種情報収集に役立ちます。